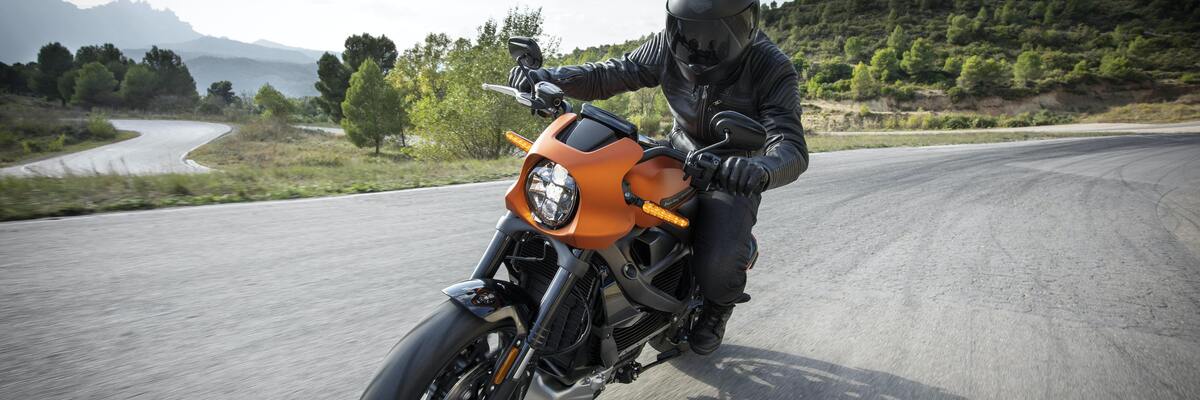
Brushless DC-Motor Driver IC Efficiently Drives Pumps in Vehicles
The traction engine in a vehicle is accompanied by tens of small-to-medium size electric motors. These motors assist in key functions such as liquid cooling and provide the modern vehicle user experience (adjustable seats, electric windows, power steering and more). Especially the key supporting motors demand both highly reliable and efficient power usage. By doing so the (battery) autonomy is extended and the carbon footprint reduced. The increasing adoption of small electric motors is further highlighting this importance.
Originating from the high-end RC toys world (cars, planes, boats…), Brushless-DC motors (BLDC) are replacing older brushed DC motors in various industries. Obvious advantages are a longer lifetime and higher efficiency, but control is more complicated. Electronic commutation requires power-drive electronics and a control system to synchronize the rotational speed of the stator's induced magnetic field to that of the permanent-magnet rotor. To further optimize cost, increase reliability and flexibility, sensorless designs omit the hall-sensors in the BLDC motor. In sensorless designs, the position of the rotor is sensed by accurately measuring the back-EMF voltage on an un-powered winding. This naturally adds more complexity to the drive electronics.
The advantages of BLDC for the automotive market was identified early on by Melexis Technologies. MinDCet was the partner of choice to implement a monolithic 40V / 3A peak sensor-less BLDC motor drivers. By integrating the sensing, controlling, gate-driver and power-stages into a single chip, a significant reduction in the bill-of-material and cost was achieved. This elegant solution continues to drive BLDC motors in volume production.
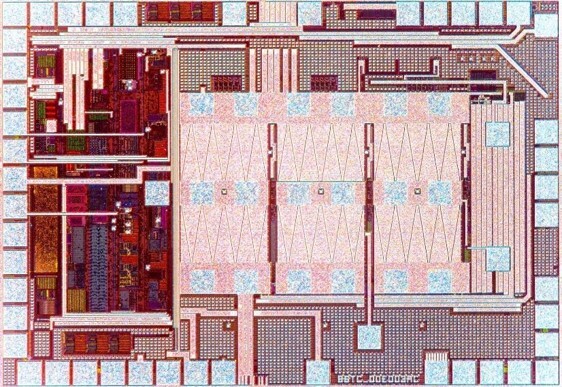